Factory Growth Edged Higher
Tenth District manufacturing growth edged higher, and expectations for future activity remained at solid levels (Chart 1, Tables 1 & 2). The monthly index of prices paid for raw materials posted a new survey record high in October, and 99% of firms continued to report higher input prices compared to a year ago. Finished goods price indexes also increased from a month ago and a year ago. Moving forward, more district manufacturing firms expected additional materials and finished goods price increases over the next six months.
The month-over-month composite index was 31 in October, up from 22 in September and 29 in August (Tables 1 & 2). The composite index is an average of the production, new orders, employment, supplier delivery time, and raw materials inventory indexes. Factory growth in October was driven by increased activity at nondurable goods plants, in particular paper and printing production, chemical manufacturing, and plastics products, while durable goods manufacturing grew more moderately. Most month-over-month indexes increased in October. Firms continued to report higher supplier delivery times, setting another survey record high. Even so, production, shipments, new orders, and employment expanded more in October compared to the previous month. Order backlog declined slightly. The pace of growth for month-over-month materials inventories eased from 29 to 20 in October, while finished goods materials inventories inched up. Year-over-year factory indexes expanded, and the year-over-year composite index moved from 48 to 50. Compared to a year ago, production, new orders, and supplier delivery time increased. The future composite index was 34 in October, near 35 in September, with the highest recorded expectations for supplier delivery time.
Chart 1. Manufacturing Composite Indexes
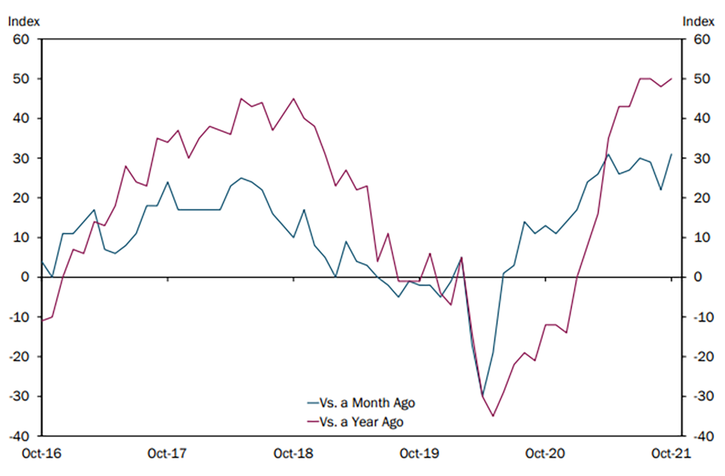
Special Questions
This month contacts were asked special questions about supply chain disruptions. 95% of firms in October reported facing challenges with supply chain disruptions and shortages, up from 89% in July 2021. Firms reported more instances of delaying projects and raising prices in October than in July, and around 70% of firms reported diversifying suppliers (Chart 2). A higher share of firms also reported increasing inventories, turning away business, and a third of firms reported making capital or technological investments in response to supply chain issues. Around 56% of firms expected rising materials prices and lack of availability/delivery times to persist for 6 to 12 months, while 36% of firms expected these issues to persist for more than 12 months (Chart 3). Only 8% of firms expected materials price increases and supply chain issues to be resolved within the next six months.
Selected Manufacturing Comments
“There is no way to increase prices enough to off-set higher costs from transportation and labor shortages and material cost increases. We expect smaller [profit] margins, with perhaps lower sales volumes, to continue to hamper our long-term sustainability as a small family company.”
“COVID variants affect overseas suppliers at different times than the U.S., in many cases extending delivery disruptions. This ripple effect on product movement will take time to recover from.”
“We currently see both increasing demand and supply chain bottlenecks occurring. Meeting increased demand will make it exceedingly hard to clear the bottlenecks.”
“Lack of transportation resources is a serious issue that we do not see being resolved in the short run.”
“We expect 2022 to be a real challenge while the supply chain rebalances.”
“We are constantly searching for hard-to-find items, we are paying more for items along with freight. We are told material that was due this month may be December; delivery is still not guaranteed. Customers understand the situation because they are experiencing this everywhere.”
“U.S. logistics infrastructure including the ports, rail, and freight were in poor shape prior to the pandemic. COVID just highlights that some major reform/improvement is required. Product delivery problems are currently masking a much larger, long term problem of workforce shortage.”
“The whole freight system is unreliable. Of course, the biggest hurdle is getting sufficient employees to man our existing production systems. The demand for our goods is excellent; we just cannot produce at capacity to meet this demand.”
“We are re-engineering finished goods to eliminate the need for parts that are shorted.”
“We are unable to pass along the higher costs to our customers and still keep their business”
“We were hit with a fee from our energy provider due to costs related to the February 2021 storm, so we will pass that cost along in product price increases.”